Industrial flue gas analysis is a legal requirement in many countries, but analyzing flue gas is necessary even in the absence of official regulations. It can save costs, reduce emissions, and ensure the quality of industrial products.
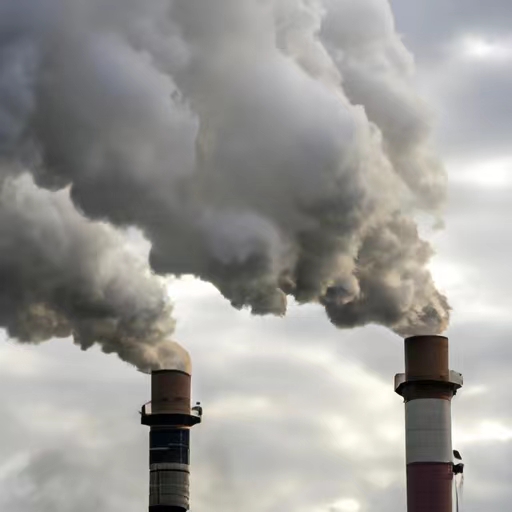
Industrial flue gas analysis involves a variety of gases, including oxygen (O2), carbon monoxide (CO), carbon dioxide (CO2), nitrogen monoxide (NO), nitrogen dioxide (NO2), sulfur dioxide (SO2), hydrogen sulfide (H2S) and particulate matter (dust, ash). Some of these substances may pose an immediate threat to human and natural health, so a clean combustion process is essential. However, this can only be achieved by regularly controlling the combustion process.
When it comes to industrial combustion, cement production cannot be ignored. Even today, they produce four times the carbon dioxide of all the air traffic in the world. If the cement industry were considered a country, it would be the third largest emitter of carbon dioxide in the world after China and the United States.
The natural raw materials for cement are ground, dry mixed, fired in a rotary kiln, cooled and then ground again. Therefore, a typical rotary kiln can produce 3,000 to 10,000 tons of cement clinker per day. This combustion process justifies monitoring the combustion process.
Harmful gases and substances can only be minimized if emissions are regularly monitored.
Therefore, industrial flue gas analysis plays a vital role in achieving environmental goals and direct cost savings.
Our AQM-09 air quality monitoring system is used for Detection of polluting gases (SO2, CO, NO2, O3, etc.) Particulate matter PM2.5 and PM10, TSP, noise, meteorological parameters (temperature, humidity, wind speed, wind direction, air pressure, rainfall, solar radiation). combined with industry adopt imported sensor technology and unique heating the dehumidification compensation device ensures data accuracy.
